Here are answers to our most frequently asked questions about Admixture scales
Are Scales more expensive to install than metered systems?
Yes they could be, the upfront cost of the equipment can be higher for the admixture suppliers and possibly the concrete producer than for a flow meter set up.
However, the ongoing maintenance costs for the flow meter systems are much higher, as the flow meters need to be serviced at least biannually and each flow meter can only be refurbished once or twice then needs to be replaced. We have estimated that the payback due to reduced maintenance cost for the admixture supplier is under 2 years.
We also strongly believe that any investment required by the concrete producers is paid back over and over, due to the improved accuracy, correct dosage and usage of admixture, reduction in non-conforming concrete and disputes, improved consistency and reliability ensuring they have confidence to optimise admixtures dose and mix costs.
How are the scales installed and who selects the location?
Installation is done by a professional serviceman or your admixture supplier, the installation can be done with minimal disruption to the concrete plant, the cut over is typically 2 to 3 hours.
The scales are situated in the most convenient location to gain access to the water line. There are times where modifications to the plant have been required, for instance a platform has been installed – the most suitable location and positioning would be agreed with the Concrete company representative.
Are there more moving parts on a weigh system?
No – there are in fact, less moving parts on the scales.
The system essentially has ball valves, an actuator and proximity switch on each hopper.
To date there has been very little maintenance required on units in the field once they have been installed. They are constructed with high quality components and have stainless steel hoppers and frames. They are incredibly robust and have a proven significantly longer life as well as lower maintenance requirements.
Flow meters require ongoing refurbishment and replacement.
Who is certified to calibrate the scales?
The admixture scales will form part of the concrete plants scale management system or process and should be carried out at the frequency required to ensure the plant is ISO 9000 compliant, calibration is legally compliant and there can be little dispute regarding what is dispensed vs the batch record.
Are Flow meters calibrated?
Flow meters are currently not calibrated in the strict compliance sense – supply companies simply do a check and issue a dosage check document which is loosely called a calibration, this is not a certified legal document.
Although the batch computer holds a record of what has been requested from the flow meter there is physically no confirmation that what was requested, is what has been dispensed.
How does the admixture scale facilitate sequential loading of admixtures?
The scales allow for the admixture to be held in the hoppers and then sequential discharge as required keeping pace with the water addition, it takes seconds to discharge (50L in under 3 sec) and will have no impact on batch cycle time.
How do you ensure dosing calibration into the same vessel, different admixtures have different S.G. and weights?
As the weigh batch computers converts from volume to mass in the mix management system and then uploaded to the batch computer in mass, mix proportions are correct as per the mix design.
Can the scales be modified to allow for large or small dose rate products?
Yes, the size and number of hoppers built into the scales are determined by the plant’s requirements, we have developed scales capable of, but not limited to dispensing 225L, 165L, 75L, 50L and 30L the various frame options allow for any combination of admixture hoppers.
Can the scales be easily modified if the plant's requirements change?
Yes, If the plants requirements change additional hoppers can be added or taken out as required (configuration is modular and easy to change).
Both systems have positives and negatives. Depending on the application and location, you would need to consider which system best suits?
This may be true as both systems do have their Pros and Cons – the scales are best suited for medium to large metro and concrete manufacture plants where the investment value is quickly paid back.
Although any system that improves accuracy and supports repeatable and reliable results improves your confidence to streamline mix designs and improves concrete quality and professionalism, scales once again in most cases would have more Pros than Cons, than a volumetric system.
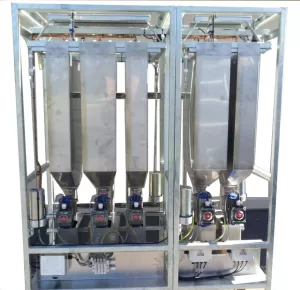
weather proof cover removed